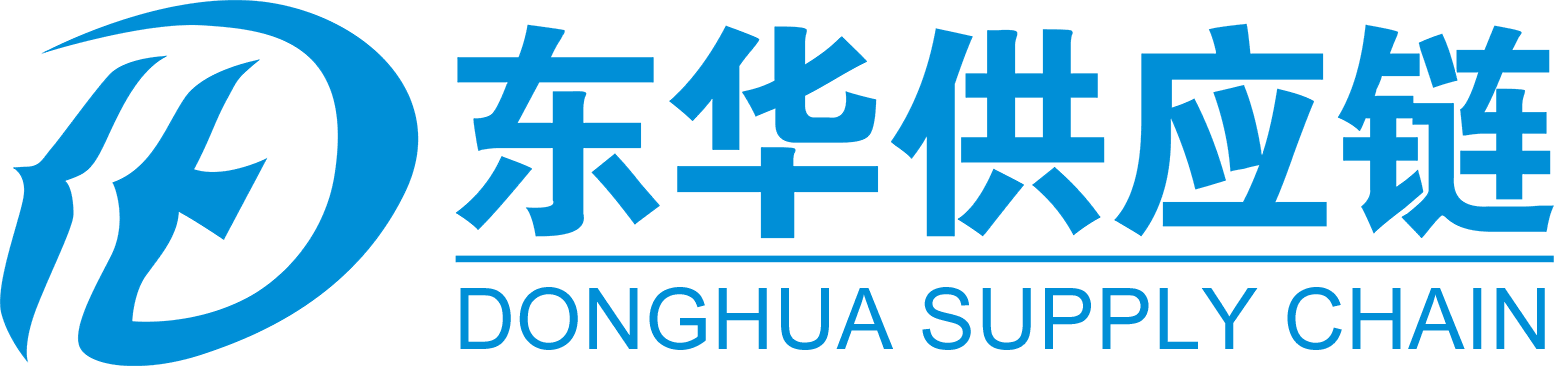
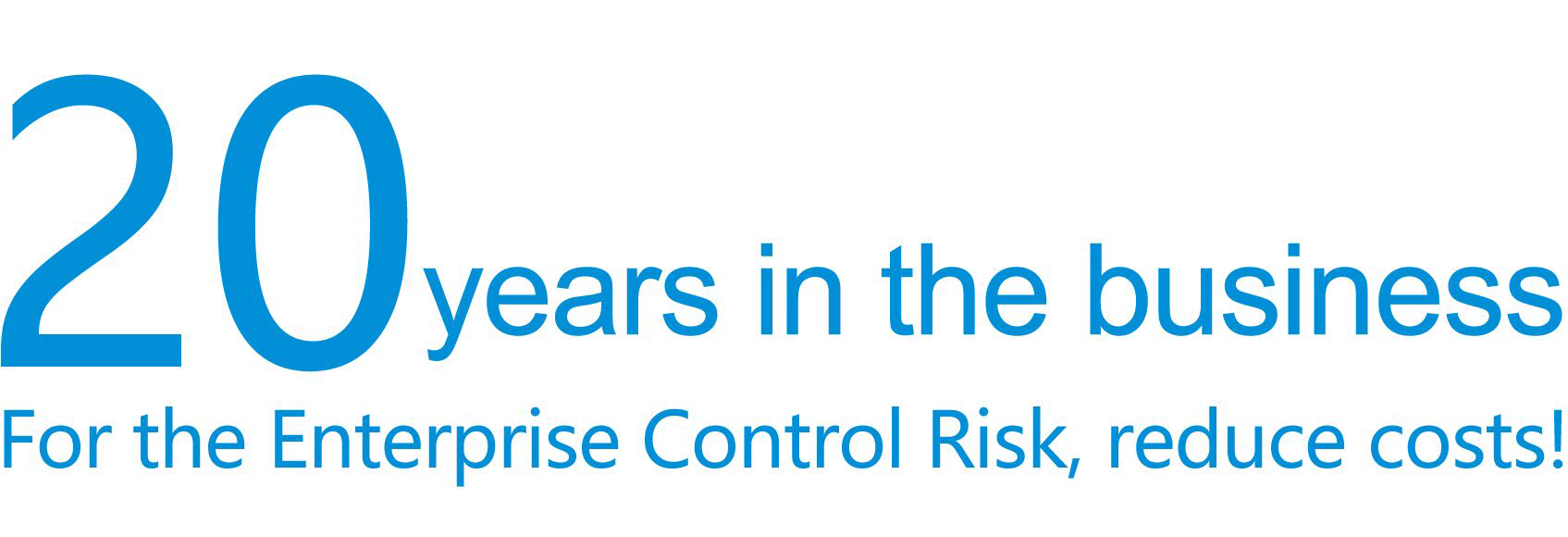
Service Time: May 23, 2016-October 31, 2016
Service team: Guangdong Donghua Supply Chain Technology Co., Ltd. Consultant Team
Leading Expert: Chief Consultant of Supply Chain Center——Jin Pengyuan
Cooperation Type: Consultation for all
clients Industry: Japanese-owned,
whether the processing and manufacturing industry has import and export rights: Is the
location of the customer: Kunshan, Jiangsu
Customer registered capital: 50 million yuan
[Customer situation]
Jiangsu Kunshan ** Plastic Products Co., Ltd. is a Japanese-funded processing trade enterprise, the factory has a total of more than 300 people and an annual output value of nearly 1 billion yuan. In recent years, due to the increase in raw material and labor costs, companies are facing increasing cost pressures, and the production efficiency is reduced, and the production process is not smooth. Japanese companies often attach great importance to lean production and process management, and pay more attention to their internal management under the increasingly severe economic environment.
[Problem Analysis]
In May 2016, the customer found the Donghua supply chain through the Internet. After several rounds of detailed online communication with sales and consultants, the company decided to appoint the chief consultant of the supply chain center-Mr. Jin Pengyuan to lead the consultant team to Kunshan to implement the project Delivery tasks.
On May 23, 2016, a team of 3 experts and consultants from our company entered Kunshan ** Plastic Products Co., Ltd. The consultant team first conducted a comprehensive diagnosis and analysis of the customer. During the implementation of the risk diagnosis process, it was found that the human resources cost was abnormal. The total number of people in this factory is more than 300, and the overtime pay of the front-line employees of the production line reached 1.23 million yuan/month. The consulting company intervened and retrieved the 6-month overtime record, conducted data analysis and in-depth research on the company, and found two problems. One is that the overtime pay on holidays is high, and the number of overtime work is more than usual, and there is usually spare overtime. No arrangement of time; secondly, the company's first-line production site management and production planning arrangements are unreasonable, and the production site management and production planning personnel are the same person. After discovering the problem, the consultant team immediately set out to formulate a rectification plan, and after discussing and passing it with the customer's senior management, the implementation plan was carried out with the cooperation of the customer's relevant leadership positions.
[Solution]
Donghua supply chain consultant team divides the production site management and production plan management into two departments for management. The consultants dictate the production site management staff, sort out standard working hours, and cooperate with the business operators through the consultants’ efforts , reducing the overtime cost of the company’s employees by 70%, saving the company about 8.4 million yuan in labor costs each year.
Then, during the coaching process, the team developed a complete set of efficient and standardized operating procedures for customers based on the actual situation of the company’s production management, which greatly saved the company’s time cost and material waste cost, and cultivated a group of excellent management within half a year Talents greatly reduce the cost of fostering standardized operations and convenience.
[Final Achievement]
In October 2016, after half a year of hard work by our consultant team, while guiding customers to actively rectify, the overtime pay alone dropped from 1.09 million yuan in May to 380,000 yuan in October, and the labor cost per month It saved 700,000 yuan, which is equivalent to 8.4 million yuan a year. In addition, after the optimization and standardization of the operation process, the customer's production efficiency has increased by 30%, which is equivalent to receiving 30% more orders under the existing investment, and increasing the income capacity by 30%.
![]() |
![]() |
Most of the companies do not understand the production site, do not understand the procurement, do not understand the production plan, do not understand the warehouse, the common cost-saving methods are to save paper, control water and electricity, these are trivial and not worth the loss, we must not It is only to help companies reduce costs, but also to help companies plan and customize, so as to truly reduce costs and increase profits from the root.
16052301#Supply chain management consulting case
Customer case
Service Time: May 23, 2016-October 31, 2016 Service team: Guangdong Donghua Supply Chain Technology Co., Ltd. Consultant Team Leading Expert: Chief Consultant of Supply Chain CenterJin Pengyuan Cooperation Type: Consultation for all clients...